Digital grid for ultrasonic testing
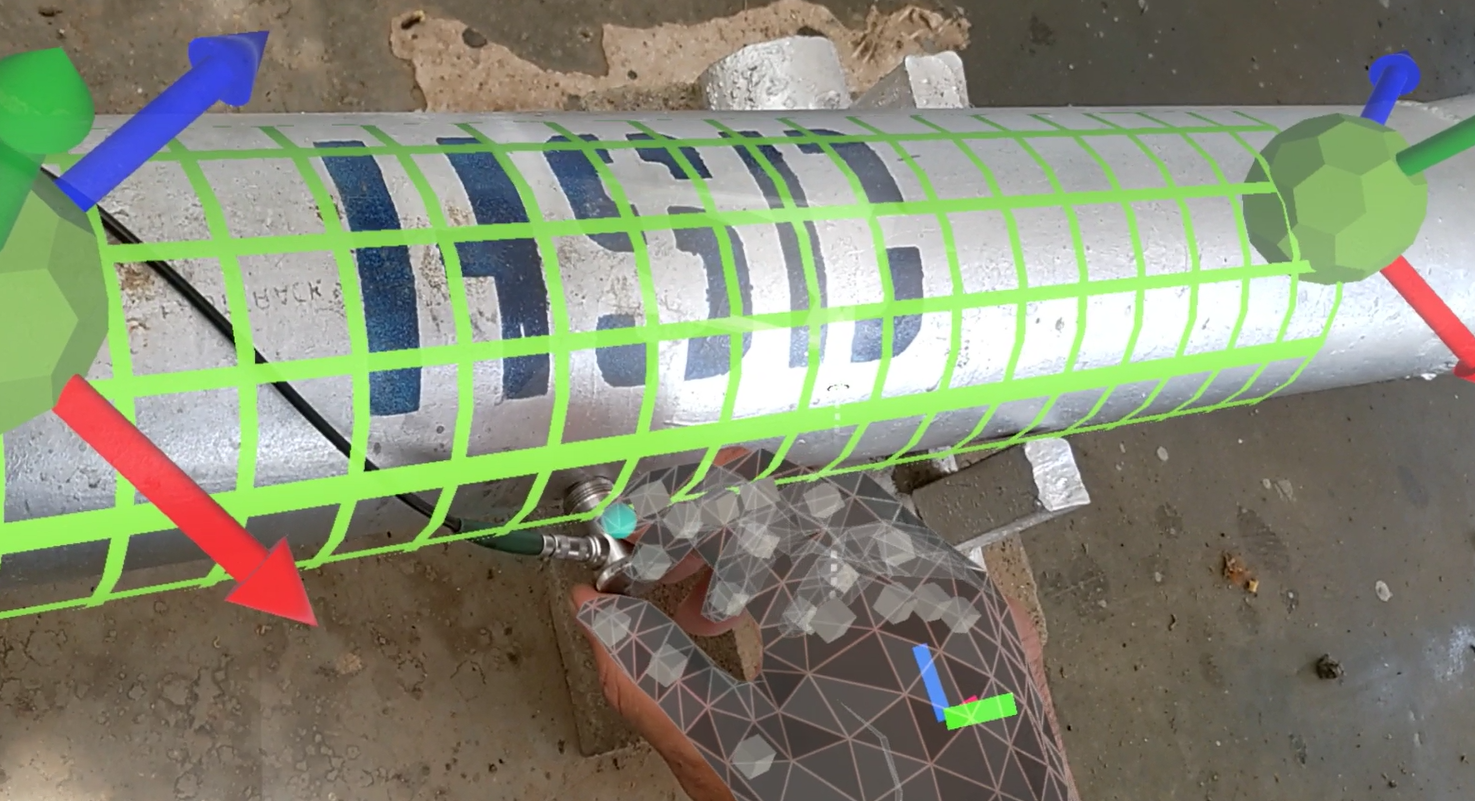
In our previous issue, we described a general application of augmented reality for NDT. In this article, we zoom in on the digital grid and explain the technology components that make it possible.
Grid for NDT — legacy approach
Non-destructive ultrasonic testing is utilized widely by industries for quality assurance. For sensitive materials or surfaces, non-contact, non-destructive testing methods are in demand. For high detectability, fine measurement grids are required. The optimal spacing of measurements depends on several factors specific to the situation:
- Pipe characteristics: Material, diameter, wall thickness all influence what flaws are most likely and how to detect them.
- Type of flaws being inspected: Smaller defects require closer spacing compared to larger ones detectable from a distance.
- Criticality of the pipe: More critical applications warrant a denser grid for higher confidence in flaw detection.
Gridding is primarily a manual task, characterized by its lengthy, tedious, and often hazardous nature. It involves physically drawing and labeling grids on the asset, guiding an inspector to specific grid locations, taking individual A-scan thickness measurements, and recording these measurements for each grid on the asset. As a result, the inspection process was not only labor-intensive but also prone to errors and inconsistencies. Plastic grid templates like this are used in certain cases which eliminates part of the problem however, it still requires keeping track of the inspected location manually.
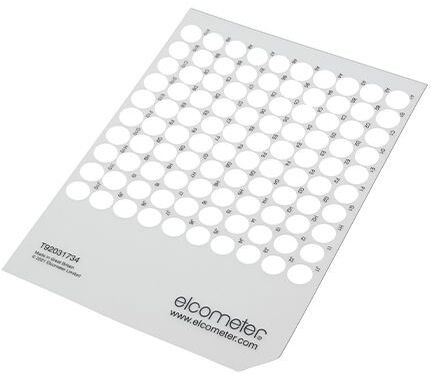
With the development of Augmented Reality, these practices shall slowly go extinct. Next, we explain the building blocks of the new approach.
3D mesh of the environment
One of AR headsets' superpowers is spatial mapping, or the ability to build detailed 3D meshes of the environment. They capture the precise geometry of a space, including the floor, walls, and shapes of intricate objects. This is achieved through a diverse array of cameras, powerful IMU (Inertial Measurement Unit) devices, and sophisticated algorithms processing the data gathered by these instruments.
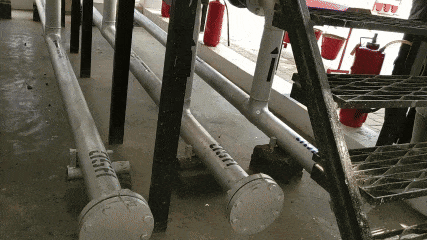
Let's take Magic Leap's documentation as guidance on how spatial mapping works. Magic Leap calls the 3D representations of your area a Space, which is made of feature points and dense mesh among other things.
Feature points are unique markers in the environment that help the device understand different areas. They include edges of the physical objects and textured surfaces. More feature points make it easier for the device to locate itself. Materials like glass or glossy surfaces may not render feature points effectively.
Dense mesh is the triangulated geometry of space derived based on the device's understanding of real-world geometry. It becomes more detailed the longer a user focuses on an area.
This matters because the first step in preparing your pipe joints or storage tanks for ultrasonic testing is finding them in space for further tracking. This is one of the crucial elements of this innovation to understand.
Digital grid
Another core capability of the Augmented Reality headset is the ability to overlay visuals on top of the physical world. Having triangulated geometry of the space and the ability to configure any digital shape through the AR headset allows technicians to create and manage the grid of any shape and size for their NDT job. Mesh of the environment will inform the location and shape of the asset while Interface controls will provide the flexibility of the grid format.
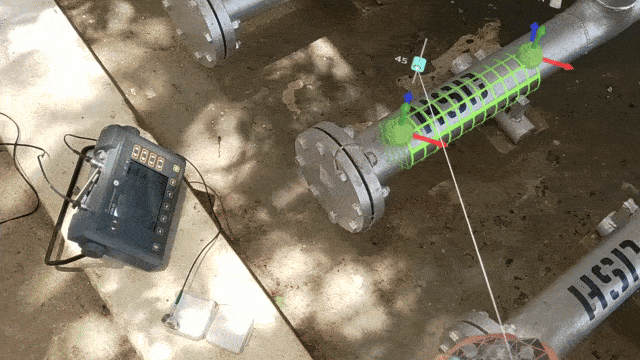
With the calibrated grid in place, you are fully equipped to take the measurements. We leave the selection of the appropriate NDT method, sensor, and interpretation of the results to the NDT professionals as we assume you are certified and know the procedures. The only requirement for the sensor to be integrated into the AR scene is a wireless module or adapter.
Upon progressing through the procedure, measurements could be saved with the reference to the location in real-time.
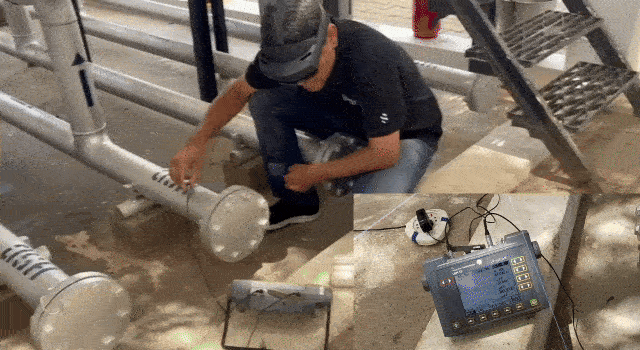
Magic Leap's sensors
The final note is on the sensors of the AR headsets that make this possible. The Magic Leap 2 device is equipped with several cameras, each serving different purposes.
- The primary video camera captures full-color RGB images and is utilized for recording real-world scenes mixed with virtual content, offering augmented reality capabilities for streaming or recording. The camera resolution is 12.59MP; it supports streaming at 4K@30fps or 1920x1080@60fps.
- The depth camera determines the distance of points in AR scenes by capturing IR images and flashing IR light to calculate depth. The camera's operating wavelength is 850nm.
- 3 Field of View world cameras are IR cameras looking at the world with overlapping views from different vantage points. This allows the system to determine the head pose at 30hz. Their operating wavelength is 420-700nm.
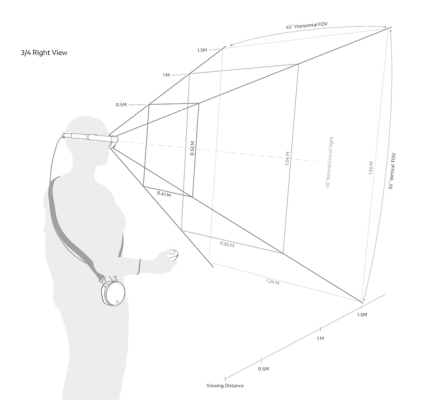
Sources
- NDT: The Complete Guide to Non-Destructive Testing 2023
- Investigation and Enhancement of the Detectability of Flaws with a Coarse Measuring Grid and Air Coupled Ultrasound for NDT of Panel Materials Using the Re-Radiation Method
- Magic Leap 2 documentation
- Hololens 2 documentation